Cyrogenic Engine
- Akshay Maheshwari
- Mar 12, 2018
- 3 min read

The cryogenic engine gets its name from the extremely cold temperature at which liquid nitrogen (the fuels used) is stored. The Space Shuttle's main engines used for liftoff are cryogenic engines. The Shuttle's smaller thrusters for orbital manuvering use non-cyogenic hypergolic fuels, which are compact and are stored at warm temperatures. Currently, only the United States, Russia, China, France, Japan and India have mastered cryogenic rocket technology.
Cyrogenic Fuels
Cryogenic fuels are fuels that require storage at extremely low temperatures in order to maintain them in a liquid state. These fuels are used in the machinery that operate in space (For example - Rocket ships, Satellites, etc.) because ordinary fuel cannot be used there, due to absence of environment that supports combustion .Cryogenic fuels most often Constitute liquefied gases such as liquid hydrogen, Liquid natural gas, liquid methane.
In a cryogenic propellant, the fuel and the oxidizer are in the form of very cold, liquefied gases. These liquefied gases are referred to as super cooled as they stay in liquid form even though they are at a temperature lower than the freezing point. Thus we can say that super cooled gases used as liquid fuels are called cryogenic fuels.
Working
Cryogenic Engines are rocket motors designed for liquid fuels that have to be held at very low "cryogenic" temperatures to be liquid - they would otherwise be gas at normal temperatures. Typically Hydrogen and Oxygen are used which need to be held below 20°K (-423°F) and 90°K (-297°F) to remain liquid.
The engine components are also cooled so the fuel doesn't boil to a gas in the lines that feed the engine. The thrust comes from the rapid expansion from liquid to gas with the gas emerging from the motor at very high speed. The energy needed to heat the fuels comes from burning them, once they are gasses. Cryogenic engines are the highest performing rocket motors. One disadvantage is that the fuel tanks tend to be bulky and require heavy insulation to store the propellant. Their high fuel efficiency, however, outweighs this disadvantage. The cryogenic engine gets its name from the extremely cold temperature at which liquid nitrogen is stored. Air moving around the vehicle is used to heat liquid nitrogen to a boil. Once it boils, it turns to gas in the same way that heated water forms steam in a steam engine. A rocket like the Ariane 5 uses oxygen and hydrogen, both stored as a cryogenic liquid, to produce its power. The liquid nitrogen, stored at -320 degrees Fahrenheit, is vaporized by the heat exchanger. Nitrogen gas formed in the heat exchanger expands to about 700 times the volume of its liquid form. This highly pressurized gas is then fed to the expander, where the force of the nitrogen gas is converted into mechanical power.
Power Cycles
There are basically 4 power cycles
Pressure-Fed Cycle
Expander Cycle
Gas-Generator Cycle
Staged Combustion Cycle
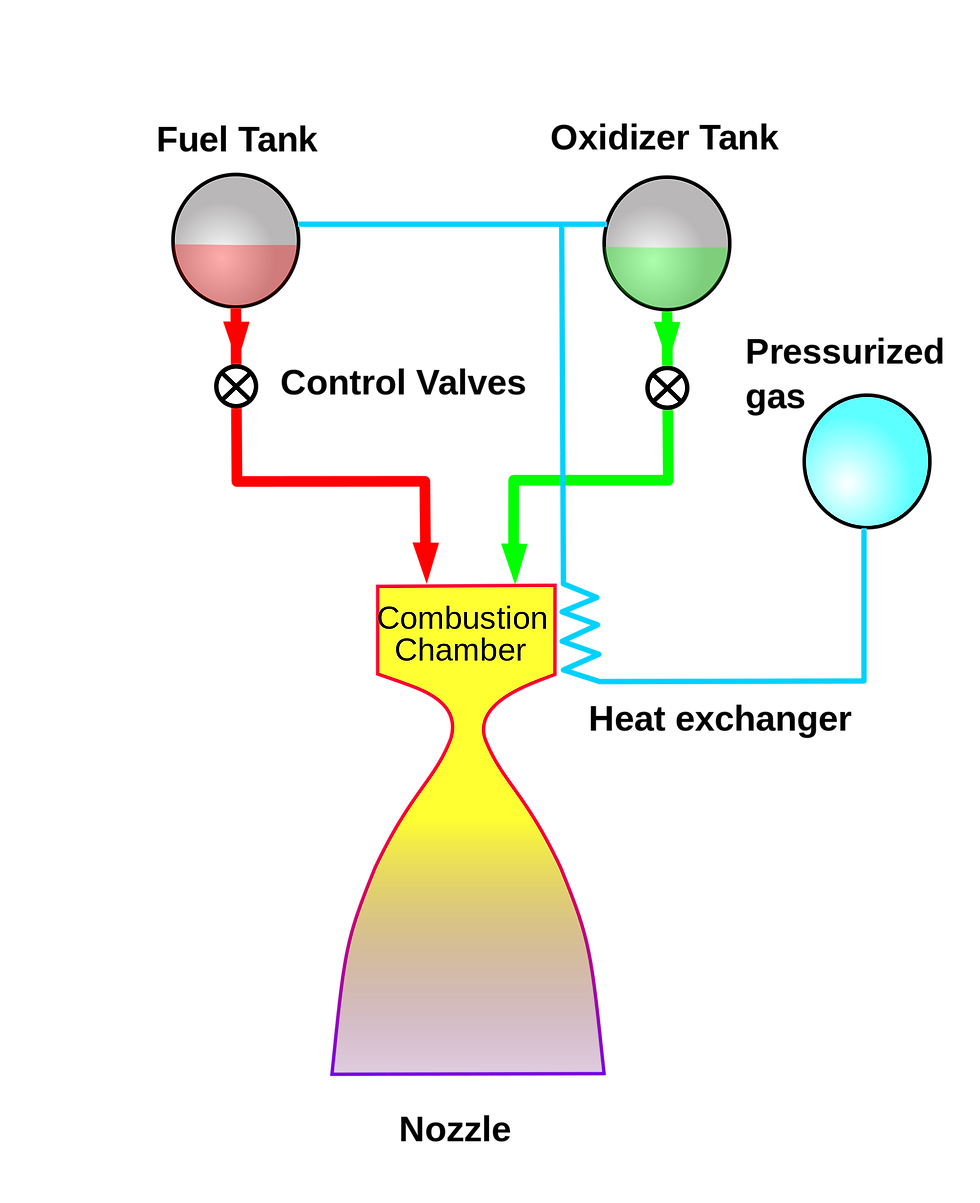
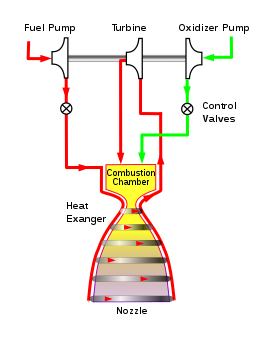
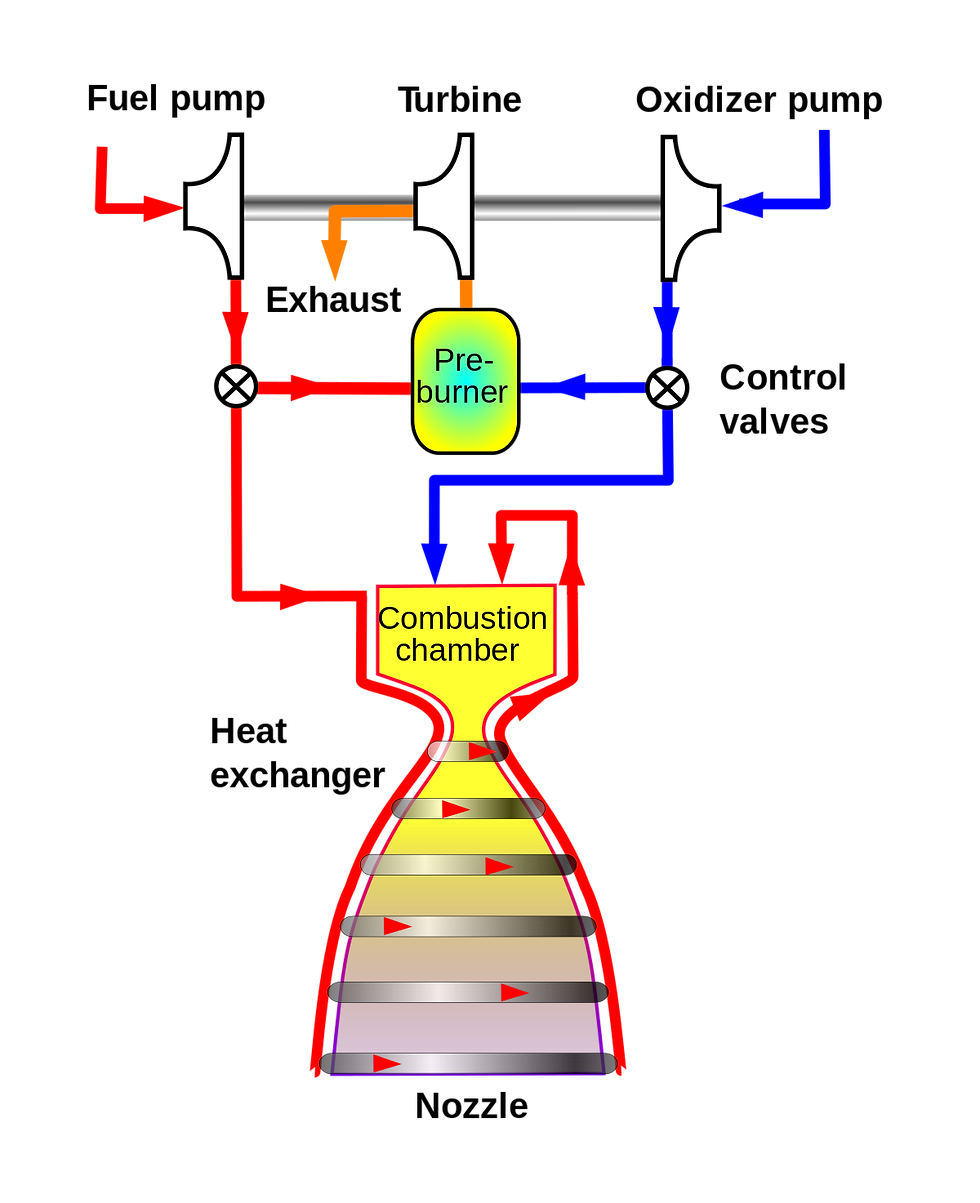
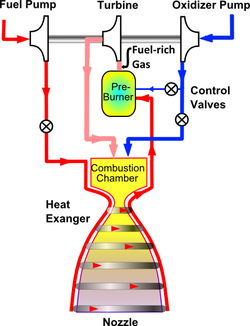
It is a class of rocket engine designs. A separate gas supply, usually helium, pressurizes the propellant tanks to force fuel and oxidizer to the combustion chamber. To maintain adequate flow, the tank pressures must exceed the combustion chamber pressure.
Pressure- fed engines have simple plumbing and lack complex and often unreliable turbo-pumps. A typical startup procedure begins with opening a valve, often a one-shot pyrotechnic device, to allow the pressurizing gas to flow through check valves into the propellant tanks. Then the propellant valves in the engine itself are opened. If the fuel and oxidizer are hypergolic, they burn on contact; non-hypergolic fuels require an igniter. Multiple burns can be conducted by merely opening and closing the propellant valves as needed. They can be operated electrically, or by gas pressure controlled by smaller electrically operated valves.
Pressure-fed engines have practical limits on propellant pressure, which in turn limits combustion chamber pressure. High pressure propellant tanks require thicker walls and stronger alloys which make the vehicle tanks heavier, thereby reducing performance and payload capacity
Comments